侯 亮 唐任仲 徐燕申
(2004年1月发表于机械工程学报 第40卷第一期)
摘要: 作为实现大批量定制生产、敏捷制造的重要一环,产品模块化设计通过对不同模块的组合实现了以有限资源生产出尽可能多的产品品种。这种设计方法已成为研究热点,并被认为是当前工程领域中最优设计的目标之一 [1] 。然而,产品模块化设计的理论研究则落后于其实践应用 [2,3 ] ,解决方案也多表现在概念阶段上。通过研究模块化设计相关文献,论述了模块化产品设计的有关概念、方法、关键技术及其应用实例;最后,提出了产品模块化设计的研究热点课题和发展趋势。
关键词: 模块化产品,模块,产品族,大批量定制,敏捷制造
0 前言
为使企业在激烈的市场竞争中处于有利地位,必须增强产品创新能力、缩短设计周期、提高用户化程度;同时又要降低成本,保证质量及良好的售后服务,传统的产品设计方法已无法满足这些要求,定制化的产品将成为未来的市场主要发展趋势。模块化设计通过产品结构、设计过程的重组,以大规模生产的成本实现了用户化产品的批量化生产及大规模生产条件下的个性化,使产品在品种与成本、性能之间找到最佳平衡点。
随着现代科技的迅猛发展,模块化已成为工程产品的主要发展趋势之一 [4] 。作为标准化的新形式,模块化被视为实现产品多样化的主要途径 [5] 及并行工程、大规模定制等领域设计实践的基本方法。本文通过文献研究,回顾、综述产品模块化的有关概念、技术及工业应用,并提出模块化产品开发的热点研究方向。
1 模块化产品概念及其工业应用
功能和结构分析是产品设计的基础。 Suh 针对产品功能特点提出功能独立设计公理,指出“一个最优设计必须保持功能需求的独立性” [6] 。因此,如果可能,产品所具有的一个功能与产品所具有的其他功能将互不相关。对产品功能独立性的研究进一步引申出对产品结构体系及功能-结构相互关系的研究,这也是进行产品模块化设计理论研究的基础。
1.1 产品模块化的概念
模块化一般指使用模块的概念对产品或系统进行规划和组织。产品的模块化设计是在对一定范围内的不同功能或相同功能不同性能、不同规格的产品进行功能分析的基础上,划分并设计出一系列功能模块,通过模块的选择和组合可以构成不同的产品,以满足市场不同需求的设计方法 [7] 。
Ulrich [ 2] 认为产品模块化与设计过程的两个特点紧密相关: 1)设计中功能域与物理结构域之间的映射或相似程度影响模块化的程度; 2)产品物理结构间相互影响程度的最小化。
这两点指出在产品功能分解树与结构分解树之间建立合理映射并保证结构树组成元素之间的相互影响最小是模块化设计的基本要求。基于这一观点, Ulrich 定义了三种模块化类型:部件互换模块化、部件共享模块化和总线模块化 [2] ,这三种方式描述了模块化产品中模块的基本组合方式。这些不同的模块组合方式,则是形成不同类型产品系列的基础。
模块是模块化产品的基本组成元素,是一种实体的概念,如把模块定义为一组同时具有相同功能和相同结合要素,具有不同性能或用途甚至不同结构特征,但能互换的单元。一个部件结构成为模块的条件是:部件的功能、空间以及其他接口特征存在于模块化产品的特定标准接口允许的范围内。
模块化产品设计过程中,通过不同模块的组合和匹配可以产生大量的变型产品,这种不同的组合体使模块化产品模型具有独特的功能、结构和性能特点和层次。因此,模块化产品是一种重要的柔性策略形式 [13] ,即柔性的产品设计使企业可以通过组合现有模块或新模块,以快速、低成本地生产能够适应市场和技术变化的产品。
1.2 模块化本质-产品结构分析与重组
在一定技术条件下开发一定范围的产品已成为当今的主流产品开发模式,而当设计由一个产品拓展为一组产品时,在一定结构框架基础上进行产品间相似性分析成为必需。产品结构一般被描述为功能(或功能需求)域、技术(或模块功能)域和物理(或模块)域及其之间的映射关系 [8] 。
产品设计可以认为是选择适当的设计参数(DP s)完成从功能域到物理域的映射,即 FR=A × DP ,其中 A 为设计矩阵 [6] 。
模块化设计在概念设计阶段的任务可以理解为决定上述设计矩阵 A ,完成从功能需求域到模块功能域的映射,之后在考虑模块尺寸、速度等性能要求的情况下完成模块功能域到模块域的映射。
这三种域的映射关系如图 1 [3] 所示,其中模块功能域的功能可分为基本功能 BF 、附加功能 AF 、适应性功能 AdF 、专用功能 CF 和用户定制功能 SF 五类,相应地将模块结构定义为基本模块 BM 、附加模块 AM 、适应性模块 AdM 、专用模块 CM 和用户定制模块 SM 。
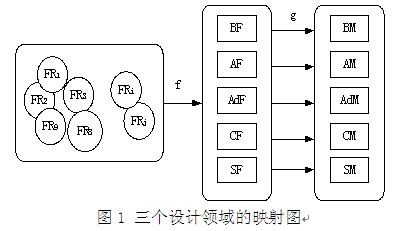
模块化程度,即在考虑品种、性能、成本条件下,产品的功能或结构如何划分或聚类,这是产品结构分析的一个重要问题。其中,模块化协调品种与成本之间的关系,集成化协调性能与成本之间的关系。因此,需要在模块化和集成化之间的寻找一个最佳的平衡点,使模块化的实施取得最佳效益。 Erens 从设计角度将产品结构分为稳定和可变部分,对稳定因素予以集成以改善成本与性能比,对可变因素进行模块化开发改善成本与品种矛盾 [9] 。一般来讲,通用模块中所占的稳定因素较多,而专用模块则是针对产品结构的可变因素而设计的。
产品结构分析的结果是完成模块化产品族的规划。产品族可定义为是一组产品,它具有相同的内部接口,这些接口在设计的各个领域(功能域、技术域、物理域)中必须为标准接口,以使产品的部件能够完全互换 [9] 。一定情况下,产品族也由一个参数化数据结构表达,当所有参数被赋予确定的数值时,可以唯一确定一个产品 [10] 。
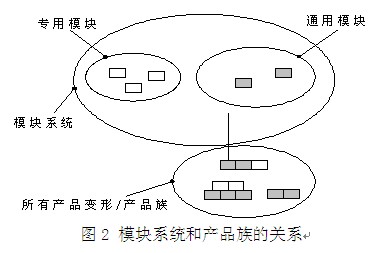
具有标准接口的可互换模块是模块化产品的基本单元,由一系列模块组成的系统就构成了模块化产品族的基础。模块化将产品划分为模块,系统地使用这些通用模块可以组成多种多样的产品。图 2 描述的就是模块系统与产品族的关系,其中通过使用模块族中的不同模块可以组合成所谓的产品系列,即产品族 [3] 。按照模块性能、结构的不同及其通用范围,产品族可进一步细化为横系列、纵系列、跨系列和全系列等几类 [7] 。
1.3 模块化在工业中的应用
模块化在工业中的应用可以追溯到 20 世纪三十年代,德国在铣床上采用的所谓积木式设计。 60 年代以后,模块化设计在国外机床行业得到普遍推广。如德国 SARMANN 公司生产的具有横系列和跨系列特点的镗铣床, WENRNER 公司生产的模块化TC500 、 TC1000 加工中心,法国 HURON 公司生产的模块化铣床等 [7] 。我国在 70 年代以后,一些企业也先后进行了模块化设计实践,如北京第一机床厂、武汉重型机床厂、天津第一机床厂等在不同程度和规模上采用了模块化设计 [11,13] ,并取得了良好的效果。近年来,随着面向大批量定制,基于敏捷制造的机床企业的兴起,模块化设计的研究和应用再次成为热点。但机床行业(也包括其他机械产品)的模块化设计并不是简单地拼装模块,机床产品具有的刚度、强度、精度等性能参数约束使其模块、接口的标准化更为复杂;作为典型的机电液一体化产品,如何从系统角度协调机、电、液等各个子系统之间的关系,也是机床模块化设计需要研究一个重要问题。
模块化设计在电子设备中也应用广泛,其中在计算机中的应用已经趋于成熟,国际化行业标准已使计算机模块可以自由互换、匹配。软件业也广泛应用模块化方法,随着CORBA 、组件技术的发展,提高了软件模块化程度。
作为汽车大批量定制生产的关键技术,汽车模块化设计正在成为汽车制造业的重要发展方向。它将进一步推进汽车工业的分工和改组,改变了传统的汽车零部件厂从属于整车厂的地位,有利于整车厂开发高水平的平台,形成以汽车为主导,以零部件为基础的新格局。
另外,模块化在飞机、机器人、造船、工业汽轮机、家电等众多行业也得到广泛应用。不同的行业,虽然具体模块化实施方法和程度不同,取得成果有大有小,但作为工业界实现标准化、多样化的一种主要途径,模块化的研究和推广势在必行。
2 产品模块化设计方法与关键技术
Pahl [3] 将产品设计过程分为:设计任务定义,建立功能系统结构,寻找原理解和概念,选择和评价,准备布局设计几个阶段。文献 [5 ] 提出开展模块化设计的一般思路:即市场调查,技术预测,品种规划,科研先行和功能分析;认为模块化设计要依次按三个层次进行: 1)系统分析阶段(市场分析、产品系列型谱拟定); 2)模块化产品设计(系统应用阶段); 3)模块选择、模块综合模块系统设计 (详细设计阶段)。
这些研究从系统论的角度研究开展模块化设计的一般方法和过程,为针对不同的产品进行模块化设计提供了一种基本思路。
然而更多学者从产品设计的某一特定角度或阶段研究模块化的实施方法和技术。
2.1 产品模块化方法及模块识别
模块是模块化产品或系统的基本单元。因此模块化的众多理论与方法都是描述在一定条件下模块的识别方法或模块形成过程。
模块识别(或模块形成)是一个复杂、影响因素众多、多目标的综合优化过程。产品本身、客观制造环境、当前技术水平、市场需求等影响因素以及模块化实施目标都影响着具体的模块化方法。在这个过程中,相关性分析是模块识别的常用方法,即对产品基本组成单元进行定性或定量的相关性分析与计算,对这些基本单元进行聚类则形成模块。这些单元可以是产品功能或物理结构,因此,根据研究侧重不同,相关性分析一般可分为两类:以功能单元为主或以结构单元为主进行相关分析。
以功能相关分析为主进行模块划分的方法是将产品的总功能分解为一系列子功能,并按照一定的相关性影响因素进行聚类分析,如文献 [ 13] 从子功能之间的功能相关、装配相关、信息相关、空间相关的角度对功能进行分类划分。文献 [14] 提出一种功能模型定量化建模方法,将模型中各个子功能与产品中传递的能量流、物流和信号流相关联,并以客户需求程度为衡量尺度,建立需求、功能数据库,并将功能与需求的关系定量化,由此作为模块划分与模块发展的主要依据。
结构是功能的载体,功能的聚类最终还要映射为一定结构体。因此,也可以直接针对结构单元进行相关性分析,这时研究重点应放在产品结构布局和结构部件的组成及其之间的联接方式上。如考虑到产品结构在生命周期(设计、制造、装配、回收性、升级等)过程中的影响因素,通过相关分析把这些因素关联到结构单元上,利用算法把结构单元聚集成模块 [13 ~ 17] 。文献 [18] 通过在部件、模块、分系统、系统四个层次上分析产品模块化的可能性及其相应的接口约束,研究生产中企业协作关系对于模块化的影响。
图 3 概括了基于相关性分析进行模块划分原理。
矩阵分析法是相关性分析的常用算法,比较典型的是文献 [13] 提出应用 MIM 矩阵( Modular-Indication-Matrix )算法,在功能分解的基础上,首先从产品的全生命周期中确定若干可以将子功能定义为单独模块的理由,然后把各子功能依次与各个条件进行比照,确定其符合的程度,据此确定哪些子功能可分入一个模块内。模糊数学中权重概念 [16] 的引入,为矩阵分析从定性转为定量提供了依据。
另外,文献 [19] 从分析机床结构入手提出了分级模块化的概念和设想,并指出了完善模块化设计理论与方法应研究和解决的四个原则和问题 ( 分析原则,标准化原则,结合原则和适应原则 ) 。分级模块化认为,在一定级别上的模块,是由属于分级系统中低一级的模块所组成。据此,分级模块设计系统可以通过低级模块的组合最大限度地满足用户需求,然而随着模块数目的增多,模块的管理成本和接口成本也将大幅上升,因此,分级模块化在实际运用时将是非常困难的。
2.2 模块接口分析和模块组合
模块接口指模块间的结合部分,是模块组合的依据。尤其对于机械产品,如机床产品,接口部分是直接影响模块化机床性能的关键部位,据统计,整机阻尼的 70% ,刚度的 60% 决定于接口,所以对接口本身及其在模块化设计中的相关技术问题进行深入研究是非常必要的。
模块接口技术的研究主要包括两方面:一是接口本身的设计加工技术,包括接口的可靠性、可装配性、加工工艺等;二是接口的管理技术,包括标准化、编码、接口数据库管理、模块组合测试等。
针对接口面的形状与联接型式等许多学者进行了总结归纳 [12] ,并针对机床类产品总结了大多数情况下的接口几何特征图谱。另外,文献 [ 20] 提出了一种基于公理设计的接口设计方法,并用 DFMA 软件工具对接口设计方案进行评价和优选。
模块组合是根据设计任务选择出模块并组合产品总体方案。由于满足相应功能要求的模块可能不止一个,所以可能产生多个模块组合方案,使用有向图 [21] 可以清楚描述模块的组合方案。为实现计算机辅助模块组合设计,还需要合理定制模块及接口的编码 [22] 。
模块组合过程也是产品的装配设计过程。如文献 [23] 研究了模块化产品的装配设计问题,并针对模块化产品的特点提出了装配系统的设计方法;文献 [28] 研究了分布协同的网络设计环境下模块的组合方法。
2.3 模块编码
模块编码的合理与否对模块选择、模块组合以及企业的生产管理等诸多方面具有重要的影响。文献 [19] 提出了一种以 GT 编码和力流概念为基础的模块编码系统,解决了结构相对固定、接口面较为简单的模块化机床产品的结构描述问题。但其编码不能用于管理和实现模块的计算机辅助组合(CAC)。文献 [22] 对上述编码进行扩展,增加了更多有关接口面的信息描述,实现了模块的计算机辅助组合。但该编码缺乏对模块功能与结构参数的描述,无法用于针对设计要求的模块自动选择。文献 [24] 针对这一问题,在文献 [22] 编码的基础上增加了非定长的模块参数码,用于描述模块本身的性能特征。文献 [25] 在武汉重型机床厂的模块化设计中,注意到了模块编码的管理功能。
2.4 模块优化与评价
系统级的优化是对产品体系结构的优化,可使模块化实施得到最佳整体效益。模块级的优化则保证组成模块、接口及产品结构的最优性。文献 [26] 提出从属性、模块、系统三层研究模块化产品族优化问题,并讨论了优化问题的类型、目标,指出与单个产品优化不同,产品族优化要考虑并平衡模块和产品生产过程中的各种因素,建立系统成本结构,以系统运行总成本作为优化的目标。
通用性是用来评价产品模块化一般手段,它描述一个产品族中共享模块或部件通用程度的标准。通用程度可以从两个方面获得 [27] :第一,生产所有变型产品所需的所有部件 / 生产线上的所有部件,此时最坏的情况此值为1,即所有变型产品需要不同的部件;第二,产品变型数 / 所有部件数,此值越高说明通用程度越高。
3 研究热点与发展趋势
虽然模块化概念由来已久,在许多产品开发与生产活动中这种方法也被自觉或不自觉地应用。但如何系统、科学地开发模块化产品直接影响设计的有效性和最优性。而这些理论和方法的研究则落后于模块化的实际应用。
作为模块化设计的基础方法和理论,模块化表达方法与模块识别等一直是研究的热点,上文已有论述。
随着信息技术、先进制造技术等的不断发展,给产品模块化设计理论和实践应用研究提出了更多新的课题,融合、利用其他现代设计方法、制造和管理技术成为现代模块化设计的特点。
3.1 知识管理与 CAx 集成设计
产品结构、设计过程的模块化重组需要建立新的模型以管理产品知识和信息。为完全确定和标准化模块及其接口,需要描述模块以及其间相互关系的知识。模块化设计中的知识管理包括:产品、模块和接口的数据表达和组织方法及其数据搜索策略(尤其在分布式系统中),知识管理对于实现知识重用和提高模块化设计效率具有重要作用。
集成化设计是当今设计的一个热点。模块及其组合产品的设计、分析、制造等过程间的信息共享与交流,影响着模块设计、选择与组合的质量和速度。以模块为核心,研究模块化产品的CAx 集成技术正成为现代模块化设计是一个新方向,如文献 [32,33] 针对大型机械产品提出基于知识和参数化、变量化集成构建柔性模块的模块化设计方法。此外, PDM 技术的发展为模块化产品的知识管理和 CAx 集成提供了一种有效的工具。
3.2 模块化产品的网络协同设计
随着 www 技术的快速发展,基于 Internet 的协同设计技术成为可能。模块化产品的分布式协同设计为快速响应市场提供了一种更为有效的途径。分布式环境下,模块设计、管理与使用可不受地域、时间的限制,使模块的共享性、通用性得到了进一步发挥 [29] 。
关于协同设计的概念、结构、特点及其实施环境等,国内外学者已进行了较为广泛的研究 [29,30] 。但对于模块化产品的协同设计则处于起步阶段,其主要问题在于:不同供应商提供可能几何分离、或在不同平台上设计的模块,如何在此模块基础上进行设计以满足不同客户的需求。
3.3 模块化设计对先进制造技术和制造系统的影响
模块化设计与制造系统的关系也是近年来的研究热点。以模块化作为主要支撑技术的可重组柔性生产线、模块化制造系统、可重组制造系统等成为现代制造系统的发展趋势。制造系统的模块化、可重组有效解决了生产率与柔性的矛盾,并缩短制造系统重组所需的周期迅速达到规定的产量和质量,使得充分利用已有的资源,减少重组制造系统所需的费用成为可能 [31 ] 。
将模块化制造系统与虚拟制造相结合,在虚拟环境下构造制造系统,产品、制造装备及制造系统的设计均采用模块化方法,使产品和制造系统有机地统一起来,这种最优集成系统的研究将是今后的一个研究重点。
4 结束语
产品模块化设计以大批量生产的成本、质量实现产品的多样化、并满足不同用户的定制需求,因此成为实现大批量定制和敏捷制造的主要方法。然而随着应用的深入、推广以及现代信息、制造技术的发展,目前模块化技术的研究则显得不足。本文在研究相关文献基础上,总结、回顾了国内外关于产品模块化技术的基本概念及其工业应用现状,对产品模块化设计方法及其关键技术进行分析评述;最后,针对目前信息技术和先进制造技术的发展,讨论了模块化设计研究的热点和发展趋势。
参 考 文 献
Kidd P T. Agile Manufacturing: Forging New Frontiers. New York : Addison Wiley, 1994
Ulrich k, Tung K. Fundamentals of product Modularity. In: A. Sharon. Ed, Issues in Design/Manufacturing Integration, Proceedings ASME Winter Annual Meeting Conference, Atlanta, 1991 , New York: ASME, DE 39, 1991:73 ~ 80
Pahl G, Beitz W. Engineering Design-a systematic approach. London : Springer-Verlag,1996
路甬祥.工程设计的发展趋势和来来.机械工程学报, 1997,1 : 1 ~ 8
童时中 . 模块化设计原理、方法与应用 . 北京:机械工业出版社, 2000
Suh N P. The Principle of Design. Oxford: Oxford University Press , 1990
贾延林 . 模块化设计 . 北京:机械工业出版社, 1993
Suh N P. Axiomatic design theory for system. Research in Engineering Design, 1998,10:189 ~ 209
Erens F, Verhulst K. Architectures for product families. Computer in industry, 1997,33: 165 ~ 178
Ulrich Karl. The role of product architecture in the manufacturing firm. Research in industry , 1995,24: 419 ~ 440
胡维刚 . 机床模块化设计及其智能支持系统的研究与实践 :[ 博士学位论文 ]. 武汉 : 华中理工大学 ,1993
姜慧 . 计算机辅助机床模块化方案设计的理论和实践 :[ 博士学位论文 ]. 天津 : 天津大学, 1998
Erixon Gunnar. Modularity-the Basis for Product and Factory Reengineering. Annals of CIRP,1996,45(1) :1 ~ 6
Stone Robert B. A heuristic method for identifying modules for product architectures. Design Studies, 2000,21(1):5 ~ 31
Salhieh S M, Kamrani A K. Macro level product development using design for modularity. Robotics and Computer Integrated-Manufacturing, 1999,(15):319 ~ 329
GU P. Product modularization for life cycle engineering. Robotics and Computer Integrated manufacturing, 1999,(15) : 387 ~ 401
Tsai You-Ter. The development of modular-based design in considering technology complexity. European Journal of Operation Research, 1999,119:692 ~ 703
Hsuan Juliana. Impacts of supplier-buyer relationships on modularization in new product development. European Journal of Purchasing & Supply Management, 1999(5):197 ~ 209
Ito Y, Shinno H. Structural Description and Similarity of the structural Configuration in Machine tools. Int. J. MTDR, 1982,22(2):97 ~ 110
Hillstrom Fredrik. Applying Axiomatic Design to Interface Analysis in Modular Product Development. Advances in Design Automation, ASME,1994,2:363 ~ 371
[ 苏 ] Л . П . Вобрик著,李艳君 译 . 模块化设计机床布局的分析 . 机床译丛, 1983,(3):39 ~ 41
刘谨 , 陈敏贤 . 仪表车床的机床模块管理系统 . 上海机床 , 1991(1):16 ~ 20
David W. Designing an assembly line for modular products. Computers & Industrial Engineering, 1998,34(1):37 ~ 52
楼应侯 . 一种新的机床模块化设计编码方法 . 宁波大学学报 , 1998,(3):67 ~ 71
黄新明 , 冷长荣等 . 重型数控机床模块编码系统的研究 . 制造技术与机床 , 1996,(4):38 ~ 41
Fujita K. Product variety optimization under modular architecture. Computer-Aided Design, 2002,34:953 ~ 965
Erixon G. Modular Function Deployment - A method for product modularization: [Doctoral thesis]. Sweden : Royal Institute of Technology,1998
Peter O'Grady, Liang W Y. An Object oriented approach to design with modules. Computer Integrated Manufacturing Systems, 1998, 11(4):267 ~ 283
Peter O'Grady, Liang W Y. An Internet-Based Search Formalism for Design with Modules. Computersind.Engng,1998,35(1-2):13 ~ 15
Mike Rosenman, Wang Fujun. A component agent based open CAD system for collaborative design. Automation in Construction, 2001,(10):383 ~ 397
Koren Y, Heisel U, etal. Reconfigurable Manufacturing Systems. Annals of the CIRP, 1999, 48(2): 1 ~ 14
徐燕申 , 侯 亮 . 液压机广义模块化设计原理及其应用 . 机械设计 ,2001,(7):1 ~ 4
侯 亮 . 机械产品广义模块化设计理论研究及其在液压机产品中的应用 : [ 博士学位论文 ]. 天津 : 天津大学, 2002